Perbezaan utama antara PFMEA dan DFMEA ialah PFMEA membantu menganalisis potensi kegagalan proses tertentu unit perniagaan manakala DFMEA membantu menganalisis potensi kegagalan reka bentuk produk.
Kaedah FMEA (Analisis Kesan Mod Kegagalan) membantu mengenal pasti kemungkinan mod kegagalan proses pada pengurusan operasi dan reka bentuk pada peringkat pembangunan produk dalam sistem dan mengkategorikan kegagalan berdasarkan kemungkinan dan keterukan kegagalan. Mod kegagalan merujuk kepada sebarang kecacatan atau ralat dalam reka bentuk, proses atau item, yang menjejaskan pelanggan. "Analisis kesan" merujuk kepada kajian tentang akibat kegagalan.
Apakah itu PFMEA?
PFMEA bermaksud Analisis Kesan Mod Kegagalan Proses. Metodologi ini boleh mengenal pasti mod kegagalan yang berpotensi dalam proses di peringkat operasi. Secara umum, pasukan yang berpengalaman dari segi teknikal menjalankan PFMEA. Proses asas ialah mengumpul data yang mencukupi untuk punca mod kegagalan untuk membetulkan atau meminimumkan kesan mod kegagalan.
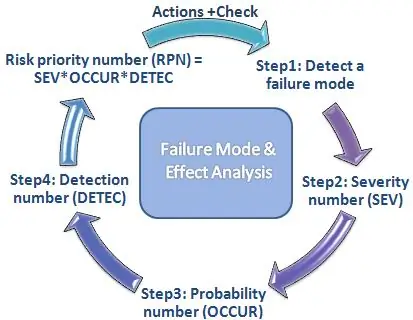
Tambahan pula, PFMEA ialah alat berstruktur yang digunakan oleh semua jenis organisasi. Ia membantu dalam membina kesan mod kegagalan dan mengutamakan tindakan yang perlu untuk mengurangkan risiko. PFMEA didokumenkan dan dibentangkan sebelum melancarkan sebarang proses baharu untuk mengurangkan potensi bahaya. Selain itu, ia juga boleh digunakan untuk proses semasa untuk mencapai peningkatan berterusan sistem.
Apakah DFMEA?
DFMEA bermaksud Analisis Kesan Mod Kegagalan Reka Bentuk. Metodologi ini membantu mengenal pasti potensi kegagalan dalam reka bentuk produk pada peringkat pembangunan. Dalam kebanyakan kes, jurutera menggunakan ini sebagai prosedur untuk meneroka kemungkinan kegagalan reka bentuk dalam situasi atau penggunaan dunia sebenar.
Jurutera alat utama untuk DFMEA ialah matriks DFMEA. Matriks ini membentangkan struktur untuk menyusun dan mendokumentasikan maklumat berkaitan termasuk spesifikasi teknikal, tarikh keluaran, tarikh semakan dan ahli pasukan. Secara amnya, DFMEA ialah kerja berpasukan kepakaran teknikal dan mungkin pasukan merentas fungsi. Selain itu, DFMEA tidak bergantung pada kawalan proses untuk mengatasi kemungkinan kegagalan reka bentuk
Apakah Persamaan Antara PFMEA dan DFMEA?
- PFMEA dan DFMEA ialah dua jenis analisis kesan mod Kegagalan.
- Langkah asas dalam DFMEA dan PFMEA adalah serupa, tetapi ia mempunyai dua aplikasi berbeza.
- Kedua-dua DFMEA dan PFMEA menunjukkan kemungkinan kegagalan, tahap keterukan risiko, kawalan sedia ada, pengesyoran dan penambahbaikan selepas tindakan yang disyorkan.
- Objektif utama kedua-duanya adalah untuk mengurangkan atau mengelakkan kesilapan besar produk dan pengeluaran.
- Metodologi ini mungkin mengurangkan kos reka bentuk atau operasi juga.
- Selain itu, beberapa kegagalan mungkin tidak dapat dikurangkan di DFMEA. Kegagalan ini boleh dipindahkan kepada PFMEA untuk mengambil kawalan yang diperlukan untuk penambahbaikan produk.
Apakah Perbezaan antara PFMEA dan DFMEA?
Perbezaan utama antara PFMEA dan DFMEA ialah PFMEA melibatkan proses manakala DFMEA melibatkan reka bentuk produk. Objektif utama DFMEA adalah untuk mendedahkan potensi kegagalan reka bentuk produk manakala objektif utama PFMEA adalah untuk mendedahkan potensi kegagalan proses. Semakan asas DFMEA dijalankan dengan menggunakan skema produk, manakala PFMEA dijalankan menggunakan carta alir proses. Satu lagi perbezaan antara PFMEA dan DFMEA ialah PFMEA berlaku pada peringkat operasi manakala DFMEA berlaku pada peringkat pembangunan.
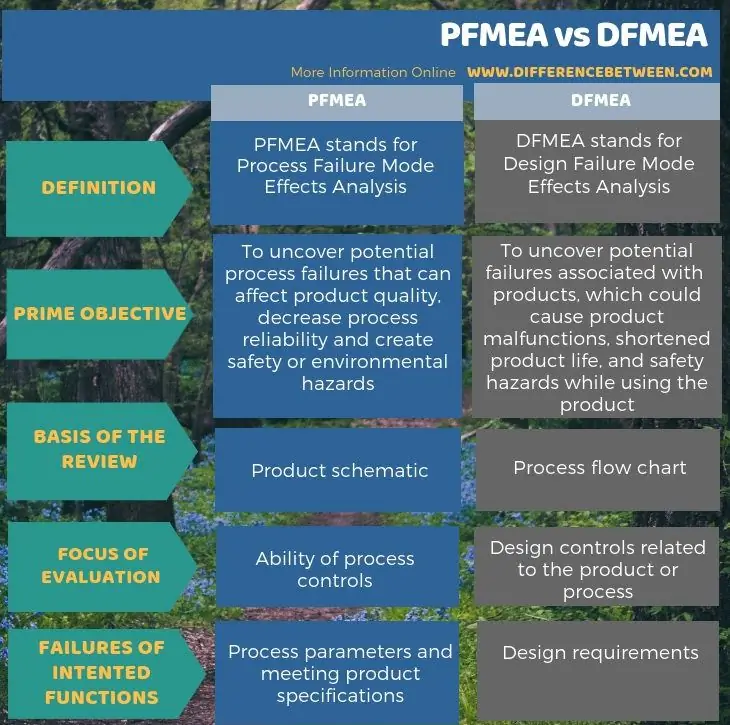
Ringkasan- PFMEA lwn DFMEA
Perbezaan utama antara PFMEA dan DFMEA ialah PFMEA membantu menganalisis potensi kegagalan proses tertentu pada peringkat operasi manakala DFMEA membantu menganalisis potensi kegagalan reka bentuk produk pada peringkat reka bentuk dan pembangunan. Selain itu, metodologi ini akan mengurangkan kos pengeluaran dan serta kemungkinan kegagalan dalam pelancaran produk.